Madas sharqi
Saudi Arabia's singature sandals
Originally made for walking in the desert, Saudi Arabia’s traditional leather slippers are used everywhere in the country. Some are still handmade by artisans, these days hailing from the South Asian community.
A large metal scissors. Punchers and sharp awls. Pliers in different sizes. A heavy wooden stump, cut off from a tree ages ago. All of it laid out on a soft carpet on the floor.
That is the workspace of Bashir, a craftsman with a small shop in old Riyadh’s Deera market. Bashir, who prefers to use his first name only, sits on the floor with the tools spread out around him. Pieces of leather, cut into different shapes and sizes, form small piles.
“The stump has been here longer than me. The man who had this workshop earlier, and taught me the craft, brought it here,” Bashir says.
“He passed away fifteen years ago. Since then, I’ve been working on my own.”
Bashir reaches into an open cupboard behind him and takes out elongated bits of cut leather. The pieces, when stitched onto a thick sole and decorated with embroidery, form the traditional madas sharqi or shibshib slippers. The sandal is worn all across the Arabian Peninsula, traditionally by men and typically along with the long thobe and red-white or plain white headdress typical of the region. Rich and poor, rural and urban – madas sharqi are used by everyone.
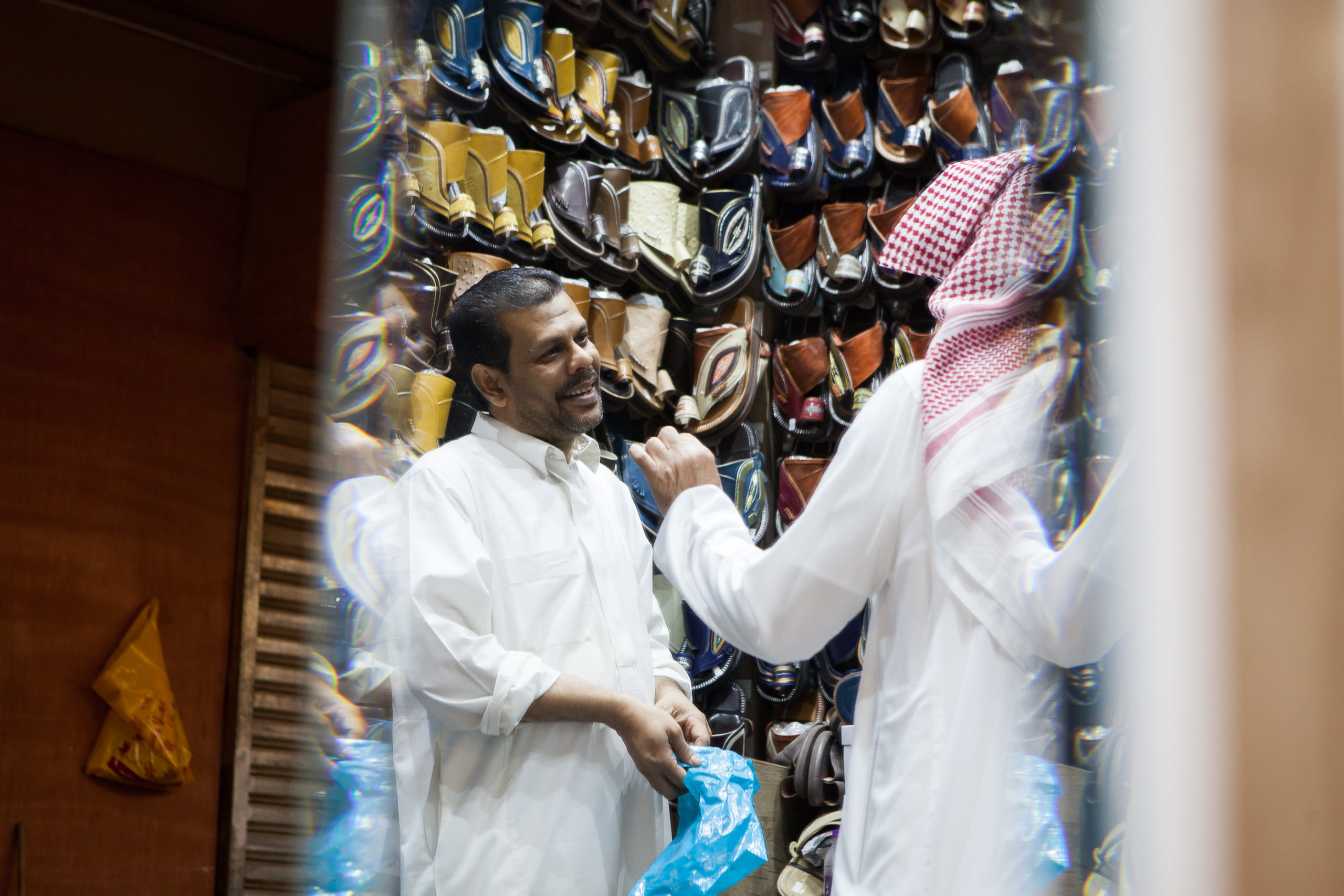
The sandals originally come from Saudi Arabia’s Najd province in the central part of the country. The Zubara tribe, when migrating from Najd to Zubair in southern Iraq, brought the craft with them, leading the sandals to become known as zubairi. This kind of cross-regional travel and exchange was common among the peninsula’s Bedouin population, who would regularly move between Saudi Arabia and parts of Jordan, Syria and Iraq.
Pieces of leather, cut into different shapes and sizes, form small piles.
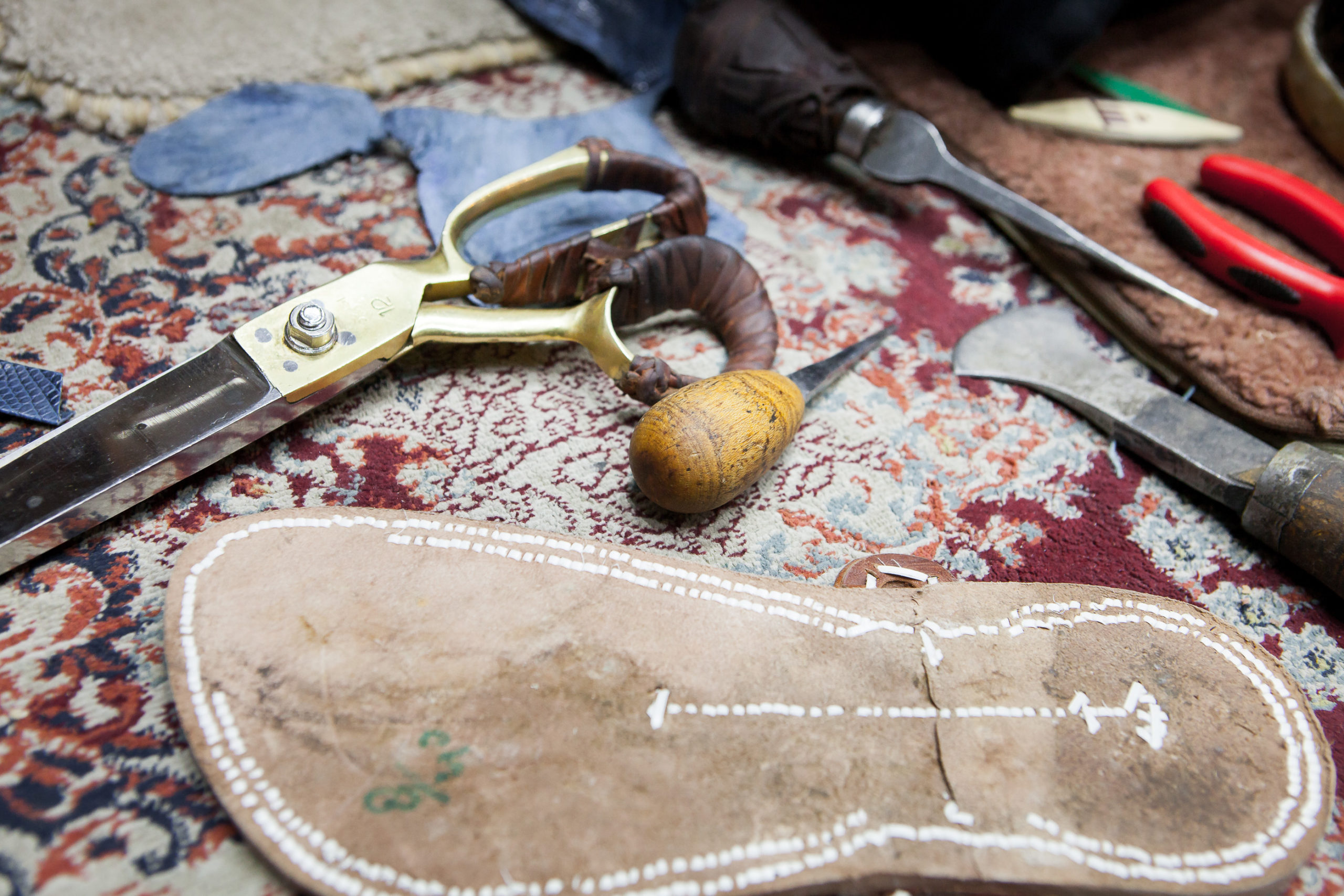
The first shoemaking Bedouins used camel leather for their sandals: a natural choice since their lifestyle depended on using locally available material, including palm fronds and camel leather, milk and meat.
“We still use camel for exclusive sandals. Believe it or not but camel leather is cheaper than that from other animals, even though the finished shoe is more expensive. That’s because it is thick and hard and much more difficult to work with,” says Bashir.
“We still use camel for exclusive sandals.”
He holds up a sole, much sturdier than all the other soles in the shop. It has been made from three pieces of thick leather, layered and stitched together.
“This sole is from camel leather, made by hand by a Saudi craftsman. But he passed away several years ago, and since then there is no one who makes them like that.”
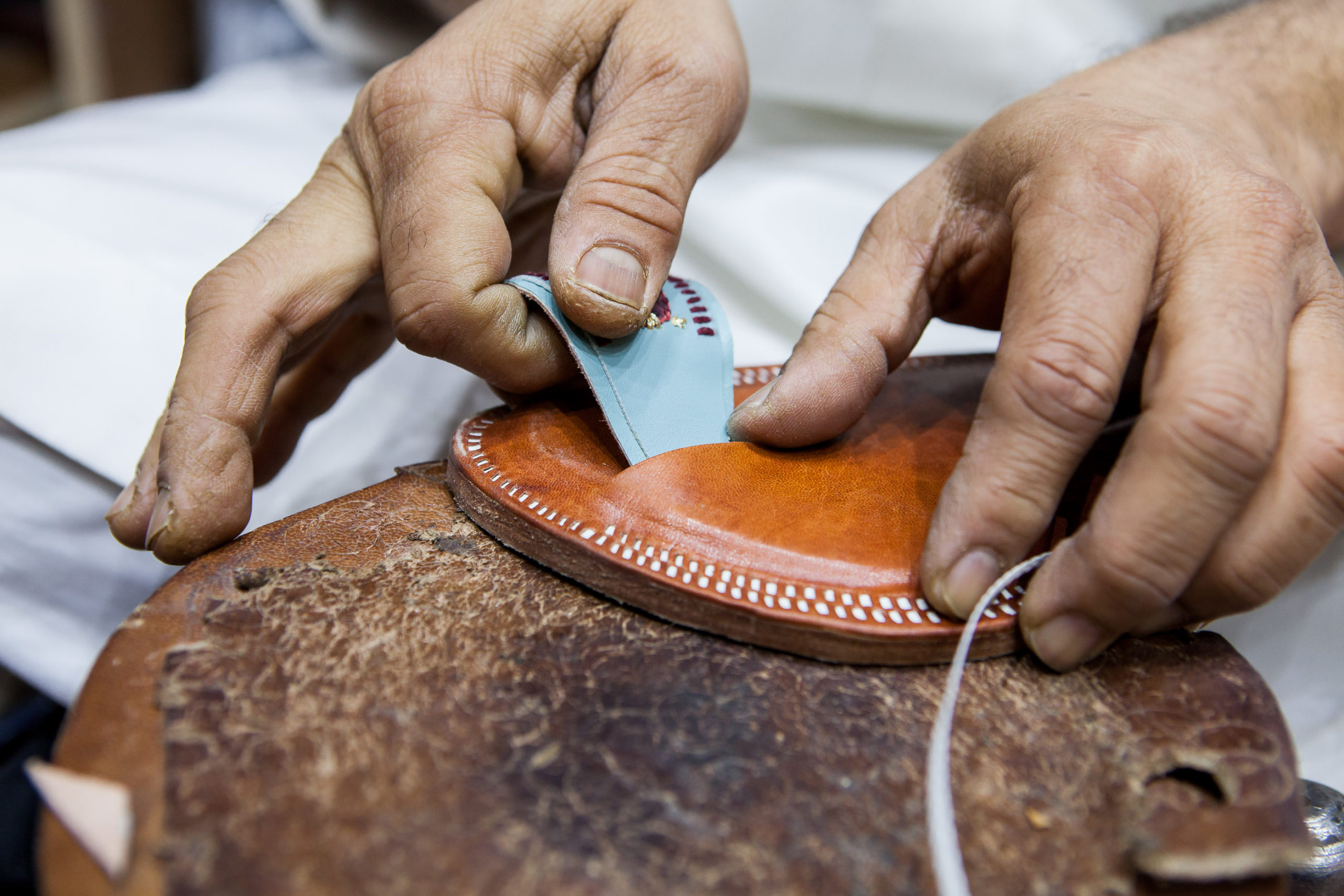
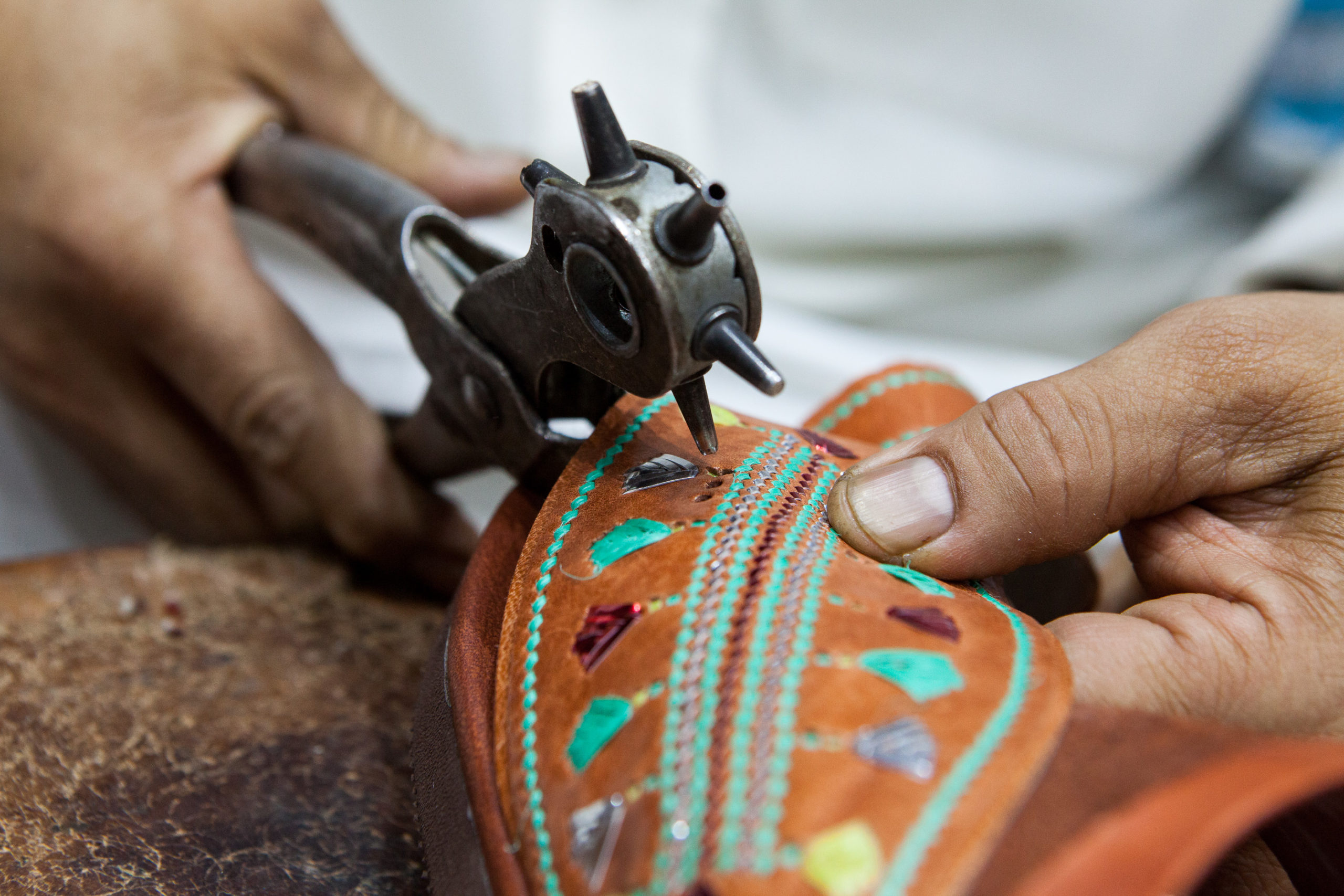
Many traditional Saudi shoemakers have now become old or passed away, without passing the trade on to others. Most craftsmen in the country today – not only shoemakers but also tailors and other artisans – hail from South Asian countries including India, Bangladesh and Pakistan.
Bashir himself is from Kerala in southern India. He has lived in Riyadh for more than 25 years, always working in the same shop in Riyadh’s market. That is how he put his three children through school.
“I visit them back in Kerala twice a year, sometimes three if I can manage. Moving here from India was a life choice I had to make,” he says.
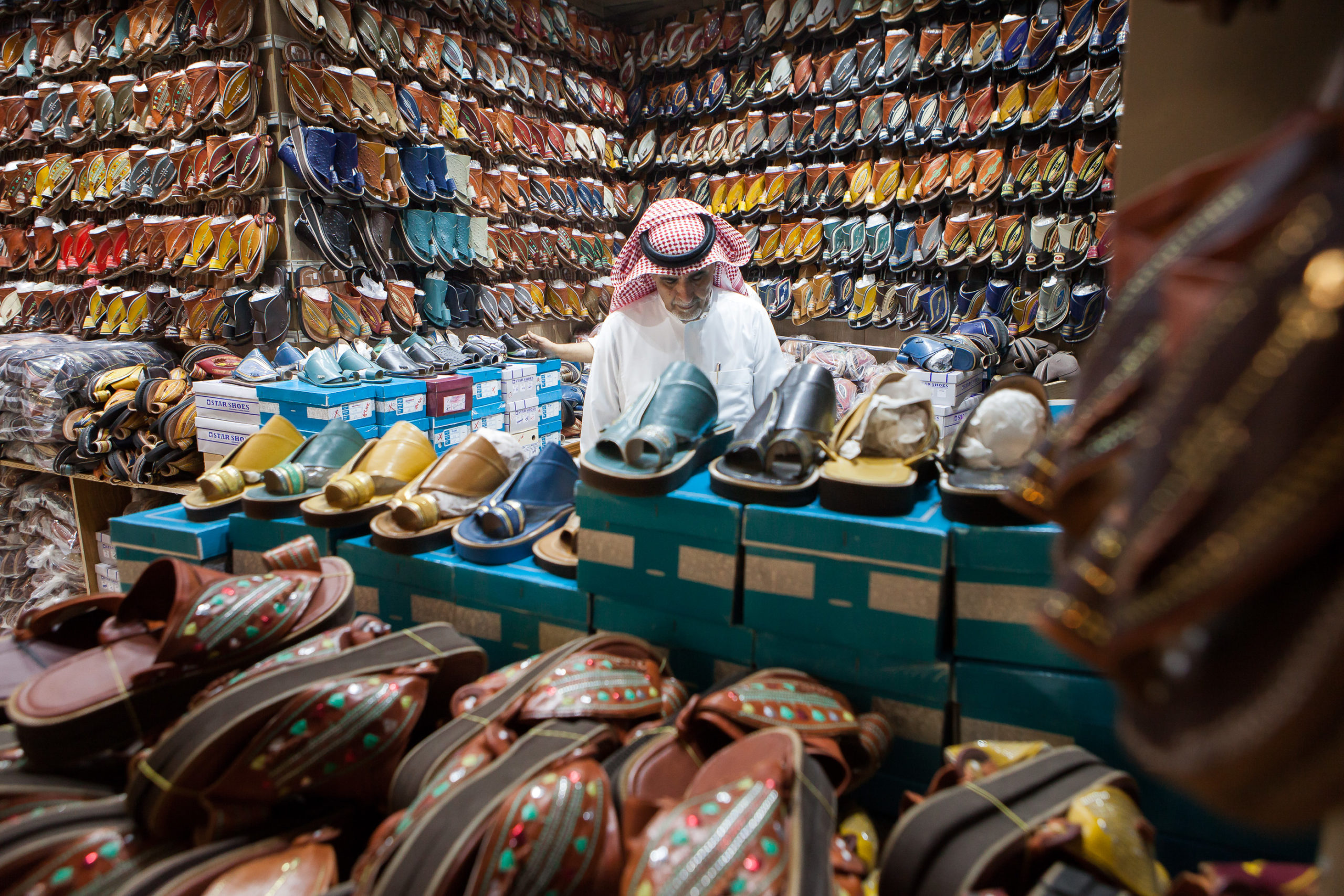
Still seated on the floor, Bashir continues to work on the sandals. He takes the scissors and cuts a piece of leather into pieces. It is done in seconds; he has more than two decades of practice. He then cuts sharp openings into the upper part of the sole, long enough to perfectly fit the leather strips. He puts the strips in place, then makes small holes in the leather with an awl. Using long white plastic strips, the kind used to wrap around cardboard boxes, he stitches the shoe together, entirely without thread or needle.
“In the past, this was done with leather. Nowadays we use plastic.”
“In the past, this was done with leather. Nowadays we use plastic. It is cheap and easy to work with. The strips are Japanese and made for this kind of use,” Bashir says.
When finished with one strip, Bashir burns the edges sealed with a lighter. The white stitches form distinct decorative patterns, typical for madas sharqi.

Besides the characteristic stitches, each shoe’s design varies. The walls in Bashir’s shop are covered with slippers on display. Shoes in deep brown leather and red-gold metallic embroidery hang next to pairs in matching shades of turquoise and blue; plain black slippers made hang alongside pairs in entirely blue or grey leather. A box near the entrance is filled with kids’ sandals sold for 25 riyals (less than 7$) a pair.
Despite the loss of an old crafting generation, madas sharqi have gained popularity in recent years. New designers have created contemporary models, aimed at customers that would not normally buy them. Saudi designer Nawal Al Maimani made pink and turquoise shoes in women’s sizes, decorated with metal studs. Monica Suitt, a Spanish designer in Jeddah, did styles in camouflage and see-through plastic.
Despite the loss of an old crafting generation, madas sharqi have gained popularity in recent years.
Traditional madas sharqi – in brown leather and embroidered décor – are still the most popular kind, and can be bought from shops and markets across the country. Many are not handmade but imported from Pakistan or India, where both material and labour are cheaper. Sometimes, the shoes are made partly in South Asia, partly in Saudi Arabia.
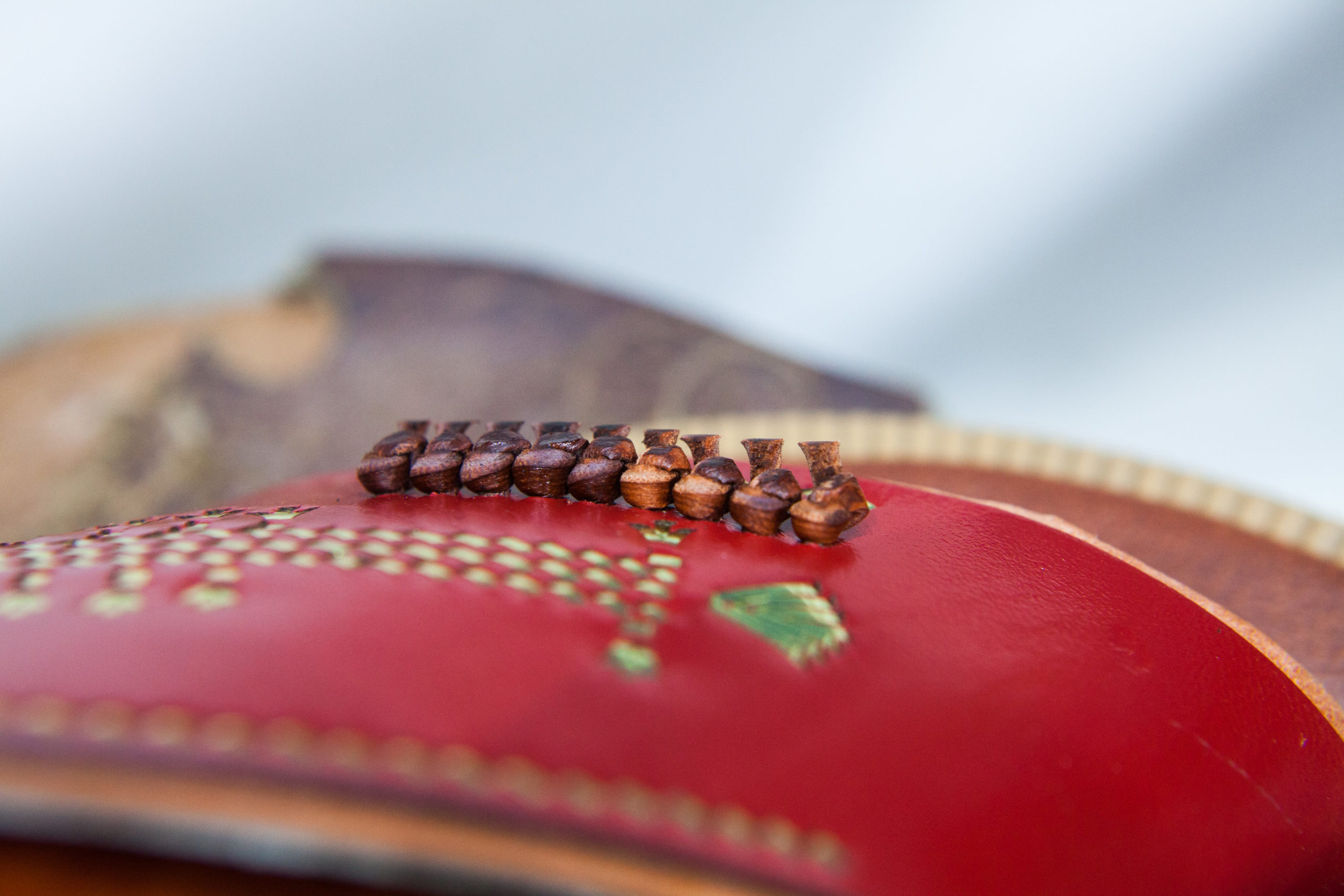
Still seated on the floor, Bashir finishes the last steps on the sandal in his hand. Using the two first fingers, he measures the length of the strap to go around the big toe. A strap for a small sandal should fit two fingers near the fingertips; a strap for large shoes should have room for them across the knuckles.
The very last step is adding the signature madas sharqi leather decoration, using thin strips of hide. Bashir takes a strip, dips both ends in water, and loops and ties a neat row of tiny knots using a metal tool.
“This stitching has two purposes. It both stitches the shoe together and decorates it,” he says.
As soon as he has put the sandal aside, he picks up another sole and starts working on the next. The production of madas sharqi continues nonstop, as it has done for ages.
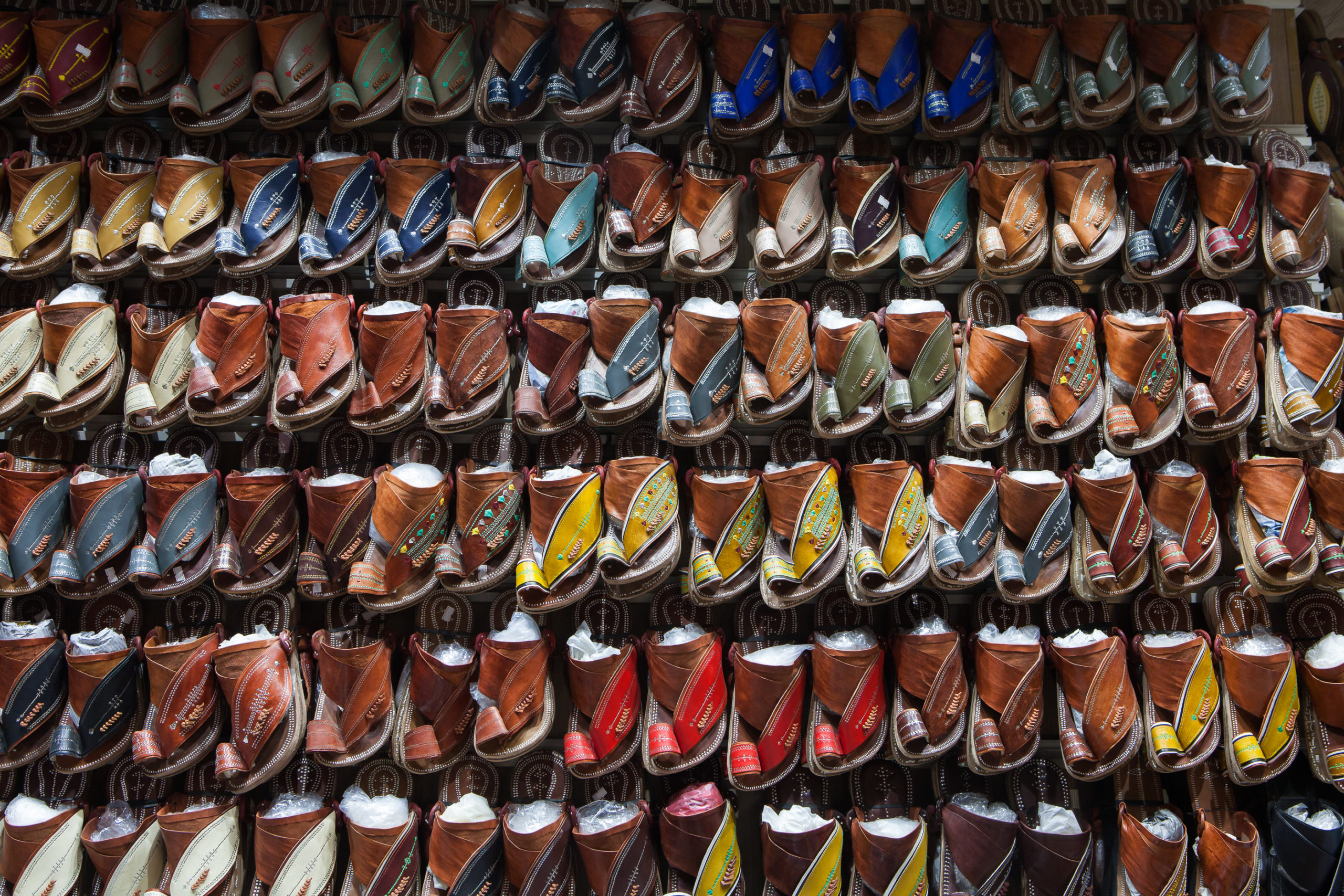